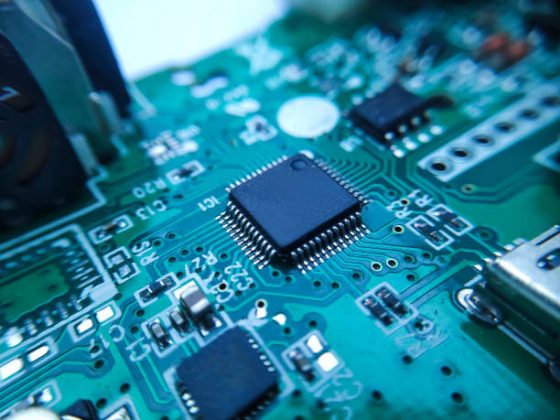
Case 01半導体・電子部品メーカーさま
超硬メタルソー/ダイシング加工
【加工面の安定と寿命の大幅向上で生産革新を実現】
お客さまの課題
・切削加工数が増加していくと加工面の形状や切幅が変化するのでできる限り維持したい。
・加工面精度とライフの向上。
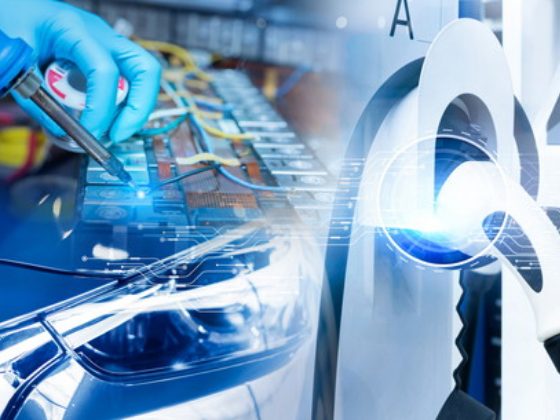
Case 02EVバッテリーメーカーさま
超硬スリッターナイフ / スリット加工
【時代の最先端が要求する精度を実現し、加工不良を大幅削減】
お客さまの課題
・はめ合いの影響から真円精度にムラが生じ、加工面に不良が発生している。
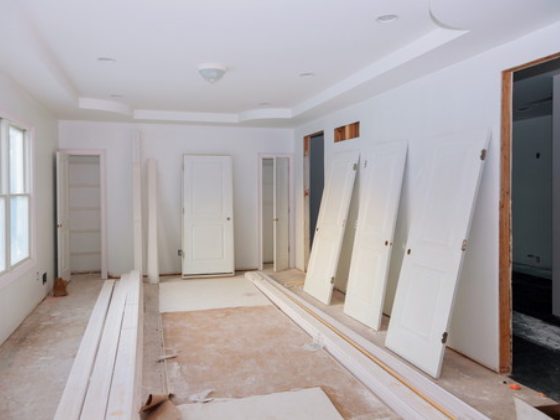
Case 03建材メーカーさま
PCDカッター / Vカット加工
【複数工程を省略し、コストダウンとV溝精度を大幅向上】
お客さまの課題
・V溝加工面の仕上がりをもっときれいにしたい。
・加工後にペーパーをかける等の二次工程を省きたい。
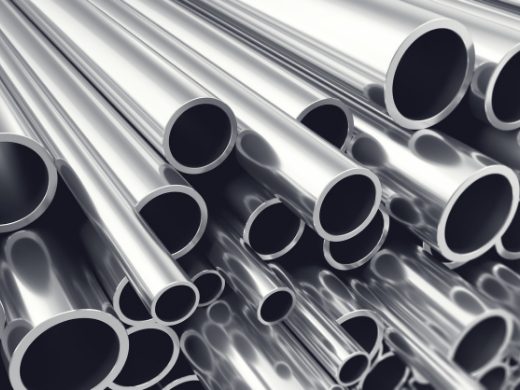
Case 04鋼材商社さま
コールドソー / 切断加工
【刃先厚みを薄くし、歩留まり率の大幅向上】
お客さまの課題
・丸棒1本から取れる歩留まりを上げたいので、もっと刃を薄くできないか。
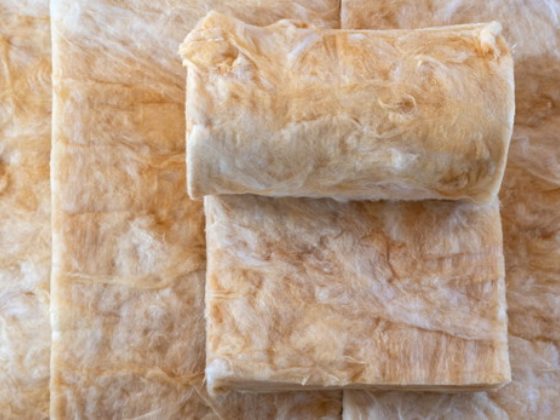
Case 05断熱材メーカーさま
大径超硬丸ナイフ(エコナイフ) / スリット加工
【エコナイフで切粉99%以上削減!コストダウンと環境貢献を実現】
お客さまの課題
・チップソーでの切断で生じる粉塵問題を解決してほしい。
・歩留まりを上げたい。
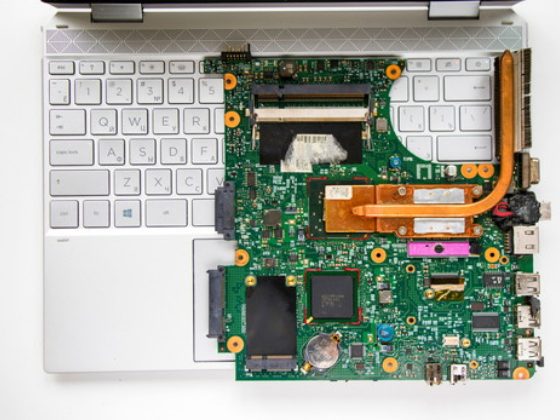
Case 06ヒートシンクメーカーさま
薄型成形チップソー / 溝加工
【革新的な刃先形状で大幅なコストダウン】
お客さまの課題
・ヒートシンクの溝が真直だとカシメ工程でカシメ部分が歪んでしまい、加工部分が安定しない。
・冷却性能向上のため、放熱板の間隔を現行よりも狭くして放熱板の数量を増やしたい。
・放熱板の間隔を狭くするために超硬メタルソーを使用しているが費用面での負担が大きい。